Case Study
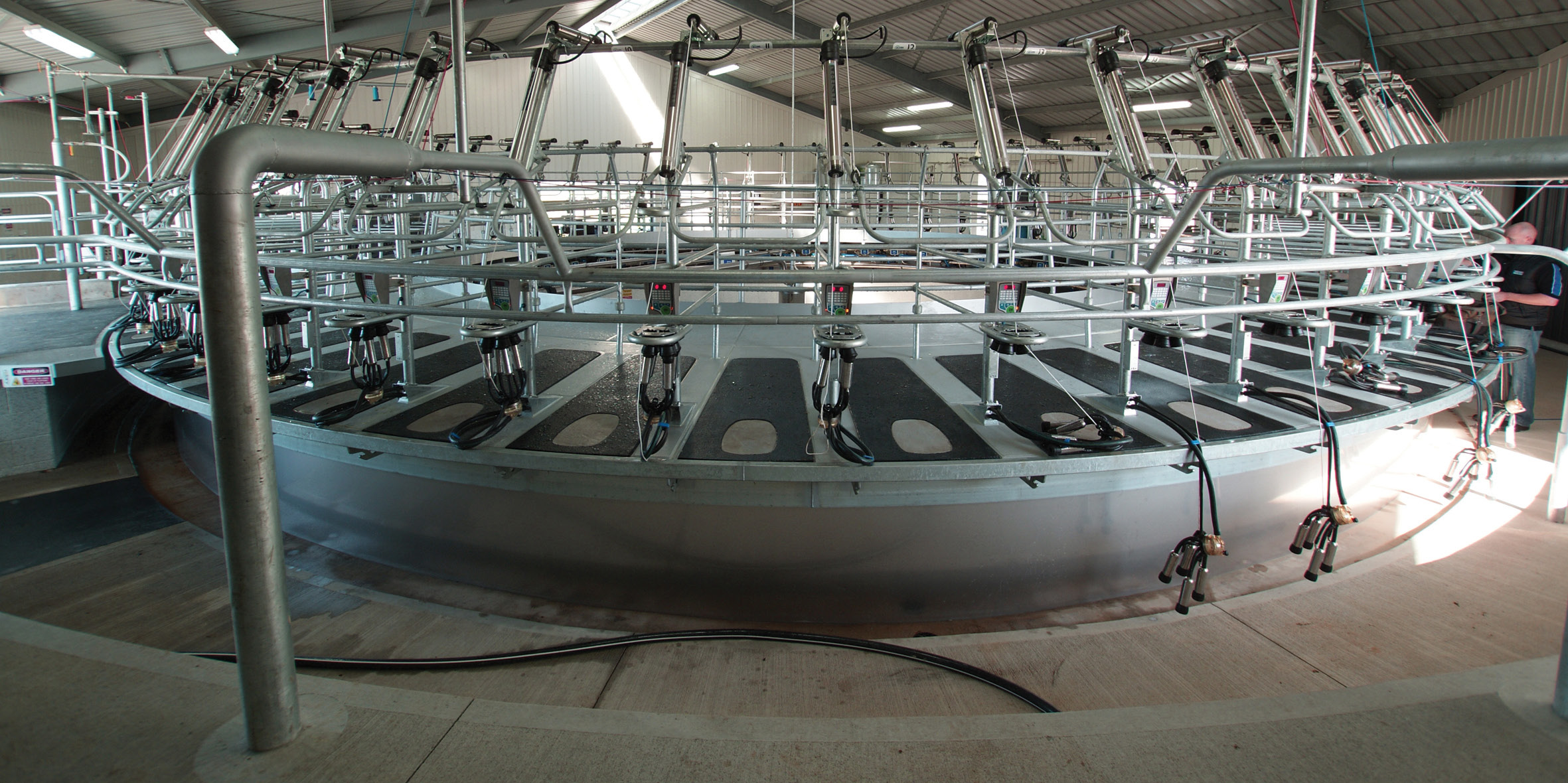
To compete in today’s world market, New Zealand, a country of just 4 million people, has had to innovate to differentiate itself from global competition, many of whom are located closer to the primary customer base.
One company that has embraced this challenge is Waikato Milking Systems. Founded in 1978, when it was a part of the plastics division of Alex Harvey Industries, the company has been through many changes, including being owned by US company DEC Corporation before undergoing a management buyout in 2001. Although Waikato Milking Systems has a 62% share of a burgeoning domestic market, with New Zealand the world’s biggest exporter of cow’s milk, it has recognised that its future growth will come from exporting its technology and equipment.
The company has four divisions, one of which is Rotary Platforms NZ Ltd. Their focus is on the design, development and manufacture of rotary platforms, which are an efficient method of milking large-scale herds, by creating a steady flow of cow traffic to cups-on. They were looking for a new approach to their products, something that would take advantage of advanced technologies and materials, and would appeal to the progressive farmers both at home and overseas. As a result, the Centrus platform was launched, which, the company claims, is the world’s first composite rotary platform for the dairy industry. The first Centrus platform was manufactured in 2009 and since then 24 composite platforms have been installed at customer sites, accounting for 8% of Rotary Platforms’ total installations. Customers to date have been New Zealand based, and tend to be younger farmers embracing new technology and looking for the most environmentally-friendly product that promises a good lifespan. The composites solution supplied by Gurit addresses these issues.
Composite materials provide a solution for the deck sections that is lighter, and indeed stronger, than the alternative concrete platforms. By replacing the concrete elements of the platforms with composites, the weight of a 54 bail platform is reduced by a massive 80%! However, the new design will still sustain rigorous use by 54 cows when fully loaded, at an average of 600kg each – a total of 32.4 tonnes! The lighter weight platform also means there is less friction on the drives and running gear, resulting in reduced wear and tear. And the composite materials offer reduced ongoing maintenance as the deck is not corroded by the cleaning chemicals or the cows’ urine.
The deck sections are constructed of a sandwich laminate, comprising a foam core, double bias and quadriaxial E-glass fabrics, reinforced with a high strength hybrid aramid/glass woven cloth, and laminated using a resin infusion process. Recyclability of infrastructure is likely to become a major driver in the dairy sector, and Rotary Platforms wants to stay ahead of the game, so they were pleased to adopt G-PET. G-PET, a recyclable structural foam core has excellent mechanical properties and is compatible with all types of composite processing. This new foam, recently launched onto the New Zealand market by Gurit, offers extremely high compressive properties, critical when you have over 400 tonnes of cattle traversing the platform daily! Rotary Platforms expects this new composite solution to have a lifespan 25% longer than its concrete platforms.
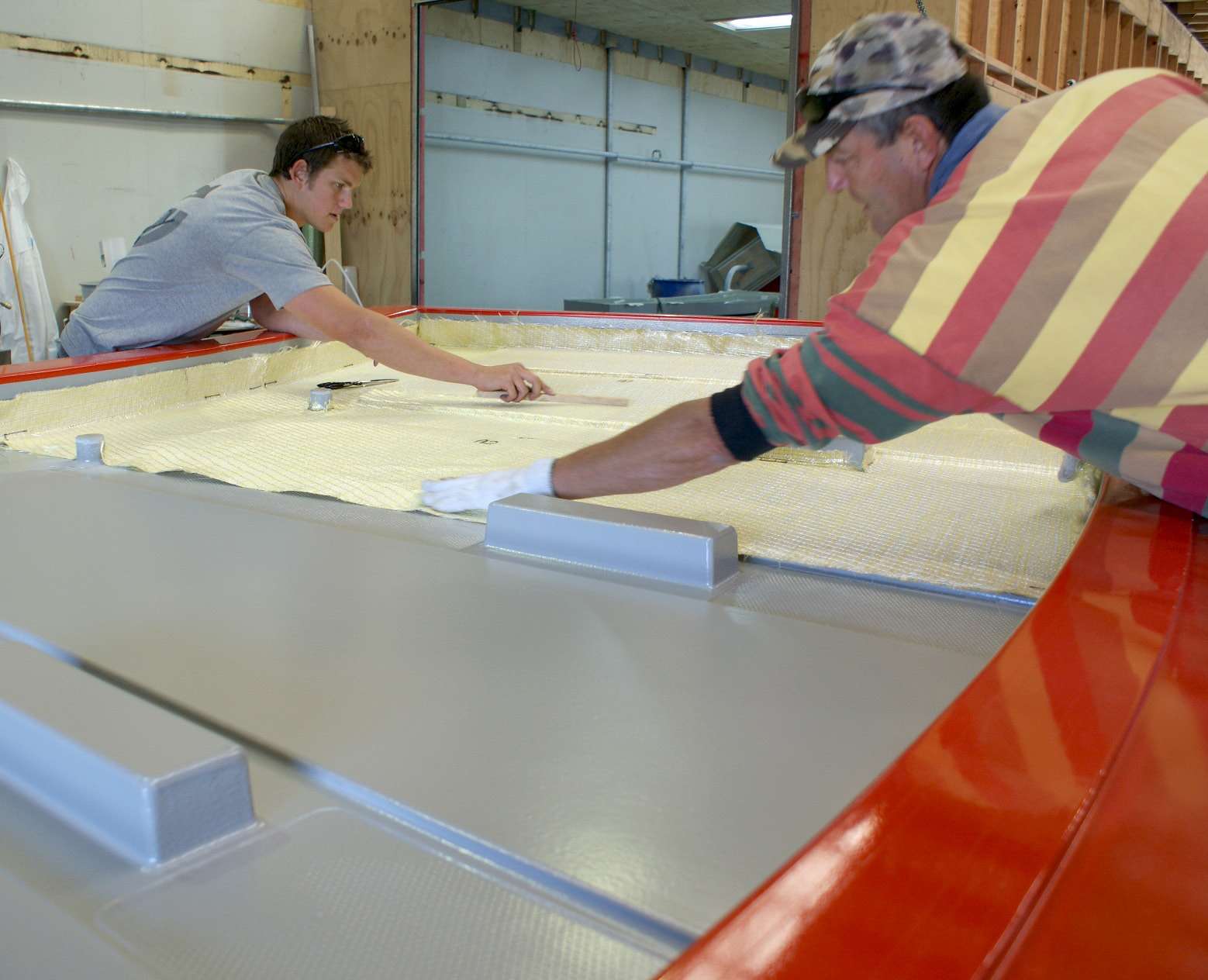
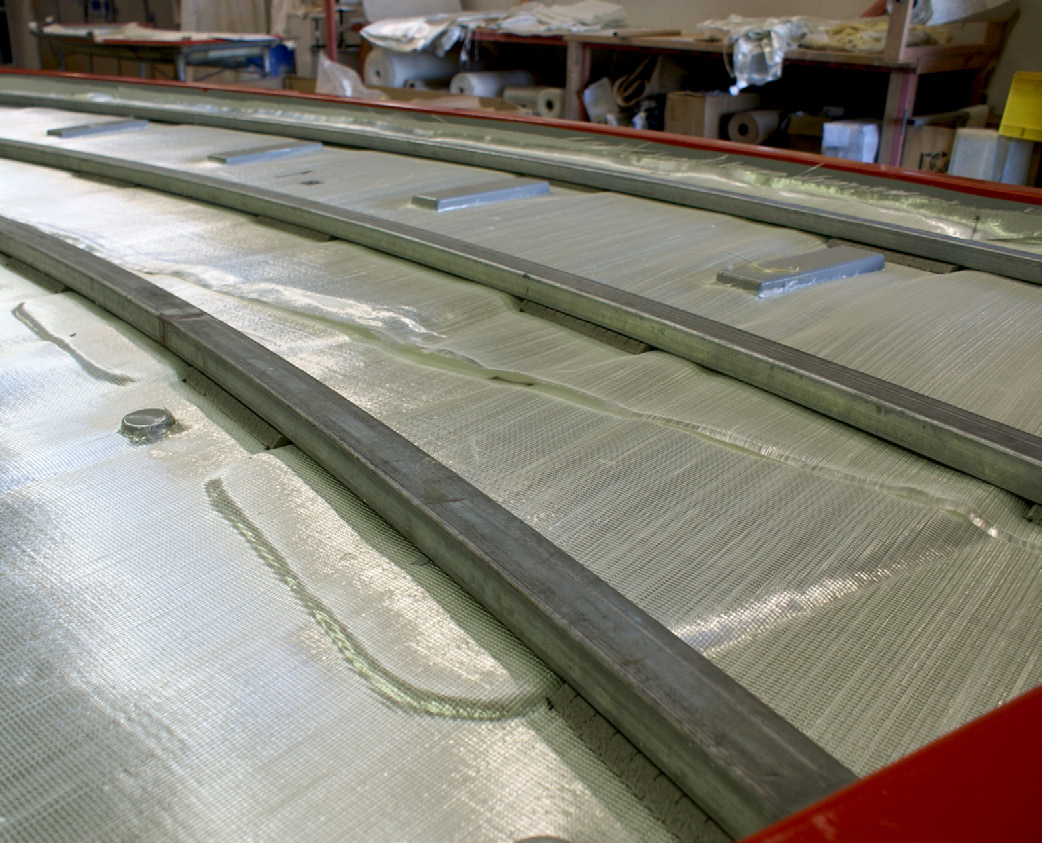
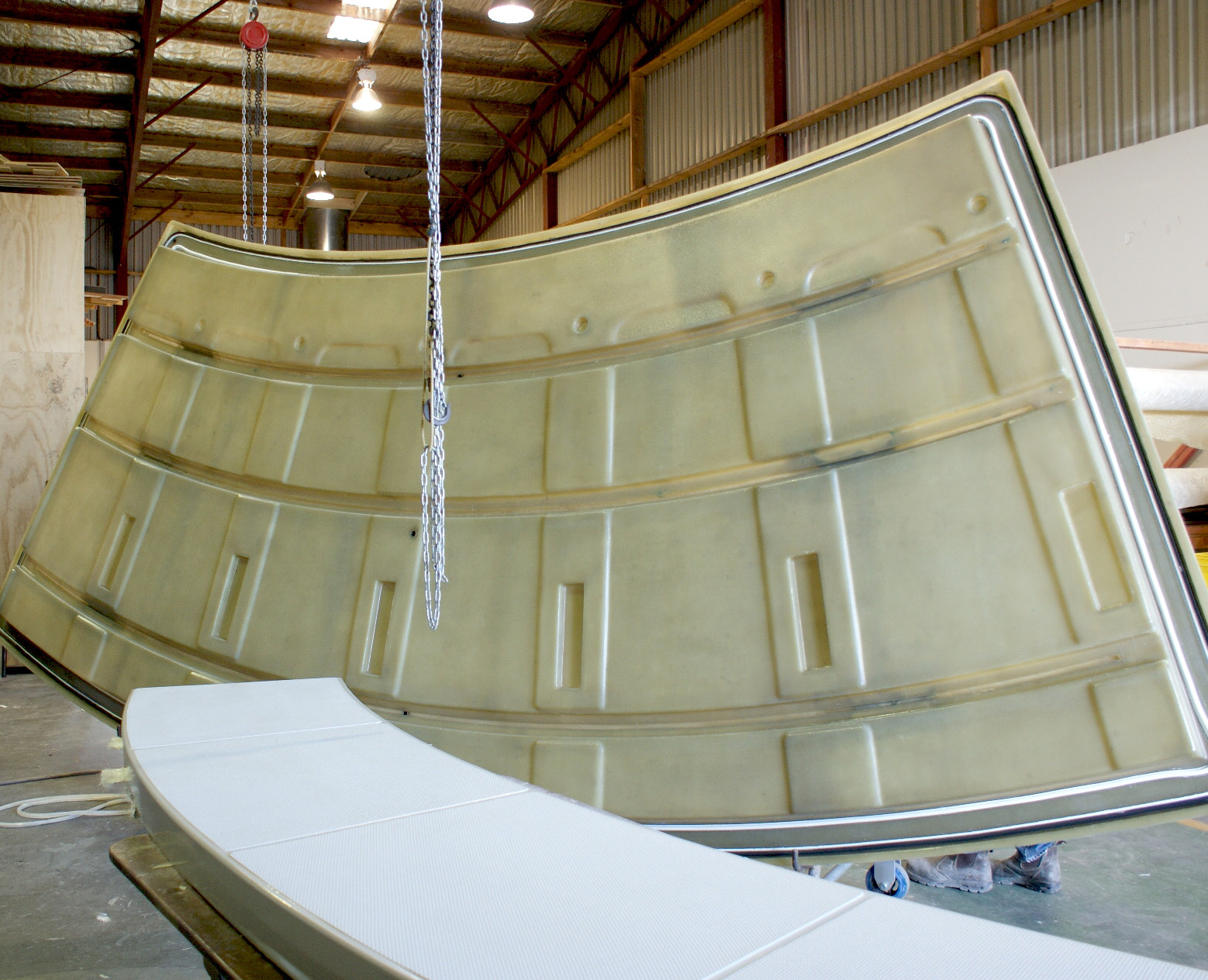
To aid Rotary Platforms in its quest for innovation, production efficiency and product quality, Gurit supplies its composite materials in a B3 SmartPac format. Each of the nine layers of material is CNC-machine cut to the exact shape and size required for the build, clearly labelled and packed in the order to be used. “We decided to use the B3 SmartPac as it eliminated the need for time consuming hand cutting at our own manufacturing facility,” says Josh Janmaat, Composite Division Manager at Rotary Platforms. “The SmartPac design and cutting process is very accurate compared with hand cutting, which allows us to apply more stringent quality controls to the finished product. A huge benefit to our customers.” The SmartPacs are provided with step by step construction guides to save time in the manufacturing process, ensure repeatability and allow efficient training of new staff.
Rotary Platforms and Gurit have worked closely to refine the SmartPac design, materials choices and construction process. “We enjoy working with the Gurit team,” continues Josh. “They are able to respond to our material supply requirements quickly as they are based locally here in New Zealand, with the B3 SmartPacs manufactured at their Auckland facility. And their flexible design team are always on hand to deal with any questions or new requests.”
As demand for environmentally-friendly, advanced technology solutions increases within the global dairy industry, and as the composite platform continues to prove a success, Waikato Milking Systems plans to export its innovation, with Australia and the UK firmly in its sights.