Structural Core Materials
Gurit is a technical leader in the development and manufacture of structural core materials. Cores in a sandwich construction are specified by designers and architects to increase stiffness and reduce the weight of a composite structure. Gurit has a range of core materials to fit any specification or manufacturing process.
PET Recycled Structural Foam
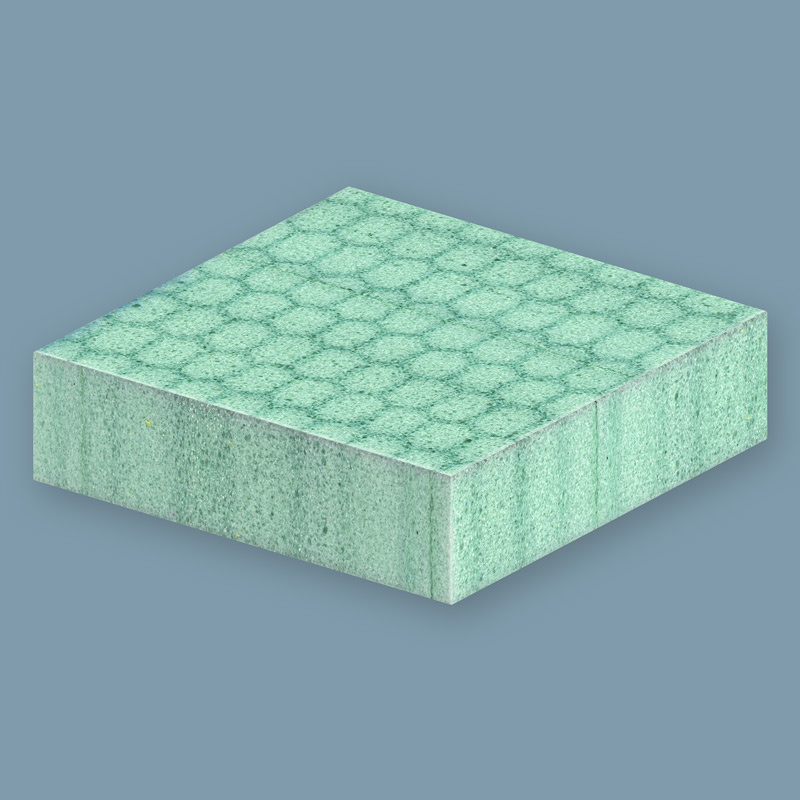
GURIT PRODUCTS/ | MAIN FEATURES | DATASHEETS |
Sustainable: Up to 100% recycled PET | ||
Sustainable: Up to 100% recycled PET | ||
*coming soon* | latest Class C - EN13501 test and certification |
Balsa Wood Core
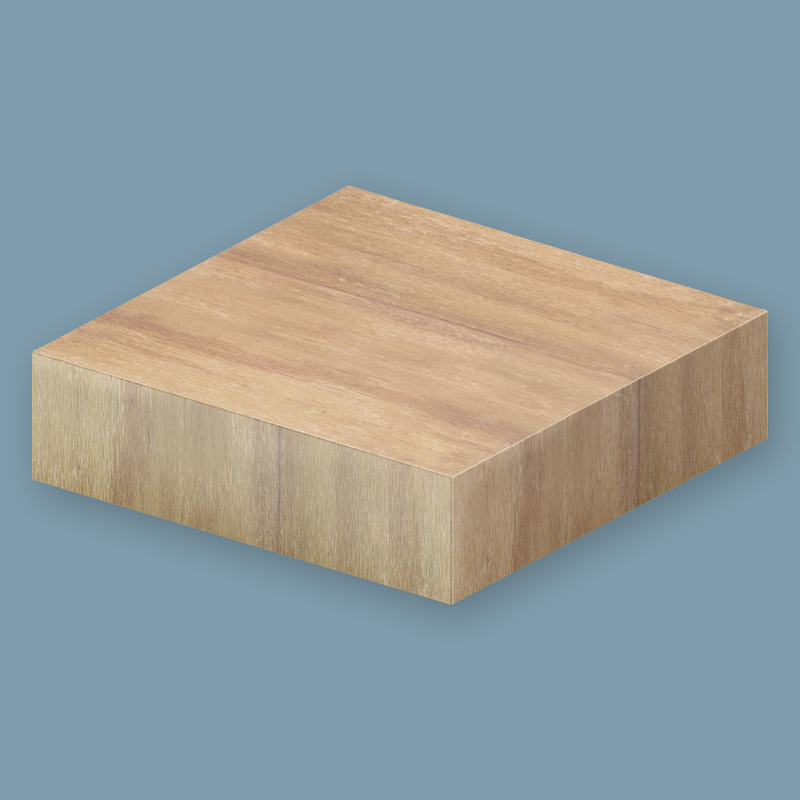
GURIT PRODUCTS/ | MAIN FEATURES | DATASHEETS |
High quality composite core material made from end-grain Balsa |
SAN Structural Foam
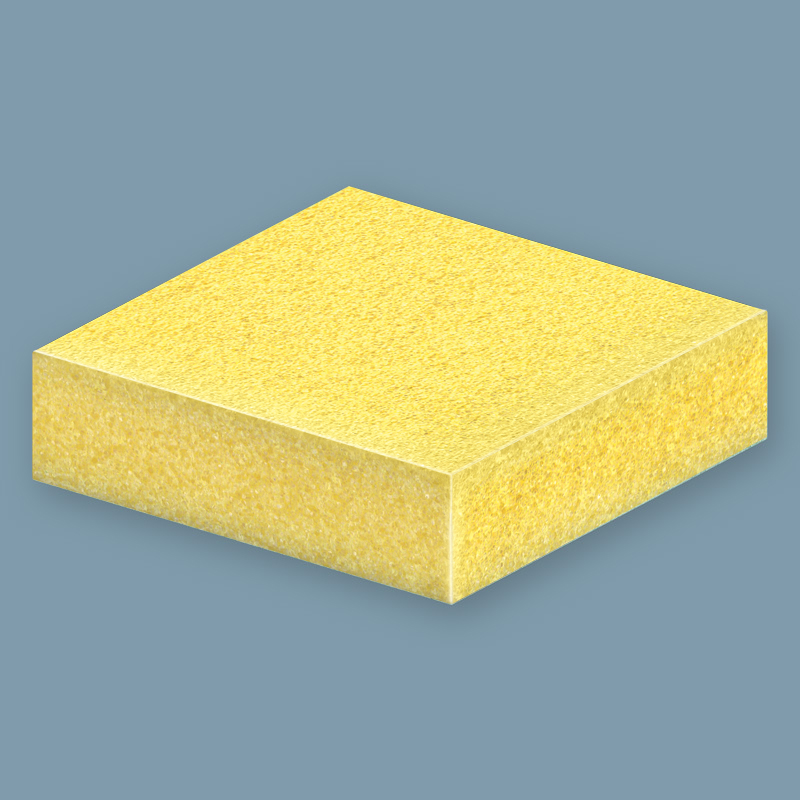
GURIT PRODUCTS/ | MAIN FEATURES | DATASHEETS | ||||||
Gurit Corecell M High performance foam, ideal for marine applications Sub-sea buoyancy foam Low resin absorption and good thermal stability in addition to the excellent handling and finishing. |
PVC Structural Foam
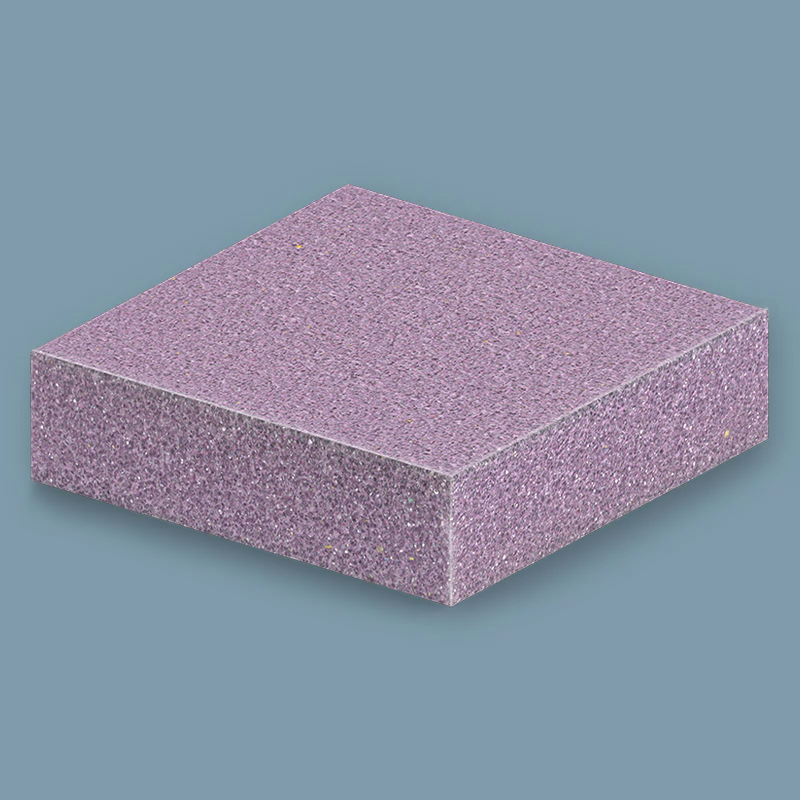
GURIT PRODUCTS/ | MAIN FEATURES | DATASHEETS |
All-purpose foam | ||
High temperature processing up to 140°C |
CORE FINISHING
Gurit standard product forms are described below. Gurit can also tailor sheets to your own specification please call to discuss your requirements.
Cuts For Conformability (Foam)
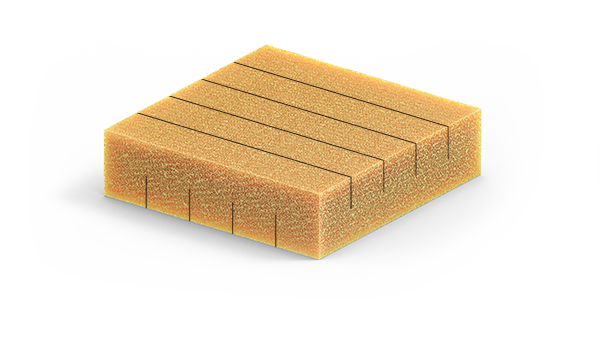
SC – Single Cut – Provides flexibility in a single direction on one or both sides of a sheet. If done on both sides, the cuts intersect so no bleeder holes are necessary for vaccum bagging. Maximum sheet size is half of a full-size sheet.
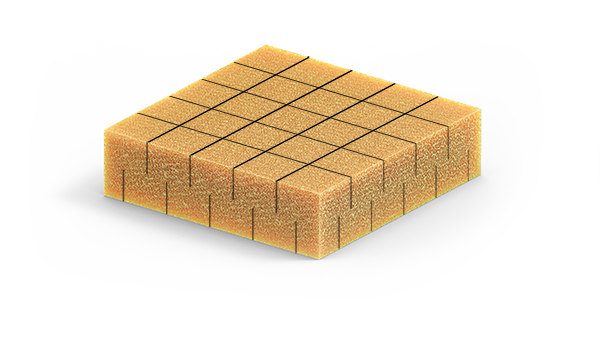
DC – Double Cut – Provides flexibility in two directions on one or both sides of the sheet. If Double Cut on both sides, the intersecting cuts make DC a highly effective resin infusion medium. The cuts are not visible when the sheets lie flat and these narrow knife-cuts minimise unnecessary resin accumulations compared to sawn core materials.
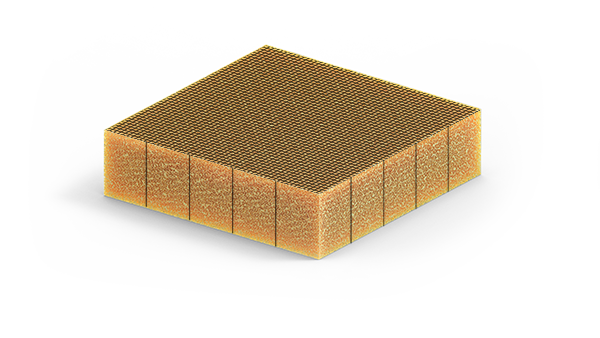
CS – Contour Scrim – provides optimum flexibility in two directions. Sheets are knife-cut in squares and bonded to a glass scrim. Available on sheets up to 25mm (0.98”) thick. Maximum standard sheet size is half the full sheet.
Surface grooves for infusion – Available on all foam types
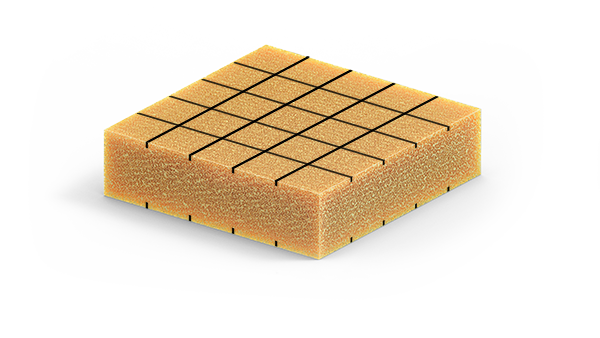
VIC – Vacuum Infusion Core There are several VIC options and Gurit can customise grooving patterns and bleeder holes as required. For curved laminate sections, double-sided DC is very effective system for resin infusion with low weight gain. Heat forming VIC surface cut also useful for obtaining curved panels with minimal resin uptake.
Combination – Combinations of these aforementioned formats are also available.
Product Formats (Balsa)
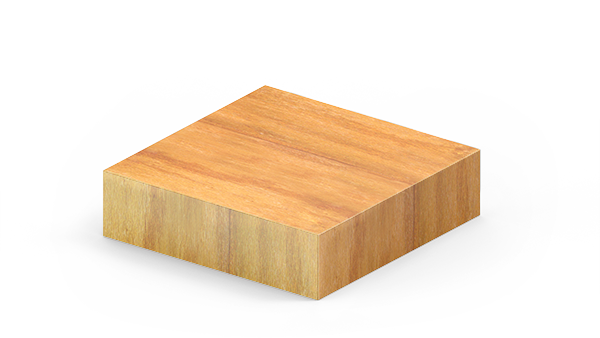
Balsaflex™ is available plain or with typical formats including perforations, microgrooves, with or without scrim, contour scrim and with optional coating.
Notice
The Company strongly recommends that Customers make test panels and conduct appropriate testing of any goods or materials supplied by the Company to ensure that they are suitable for the Customer’s planned application. Such testing should include testing under conditions as close as possible to those to which the final component may be subjected. The Company specifically excludes any warranty of fitness for purpose of the goods other than as set out in writing by the Company. The Company reserves the right to change specifications without notice and Customers should satisfy themselves that information relied on by the Customer is that which is currently published by the Company on its website. Any queries may be addressed to the Technical Department.
Wind Blade Kitting Services
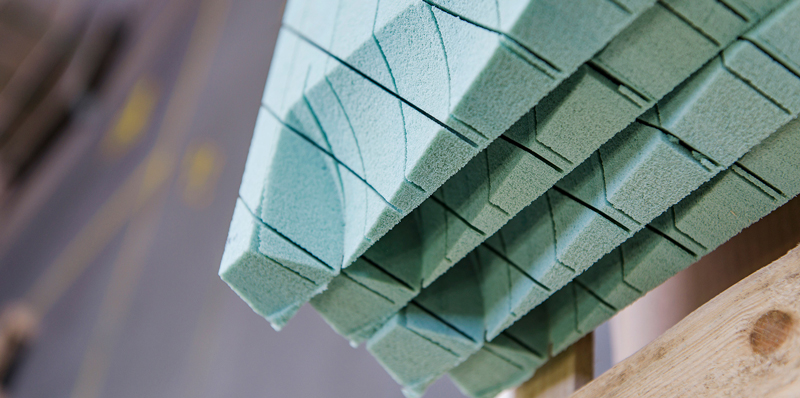
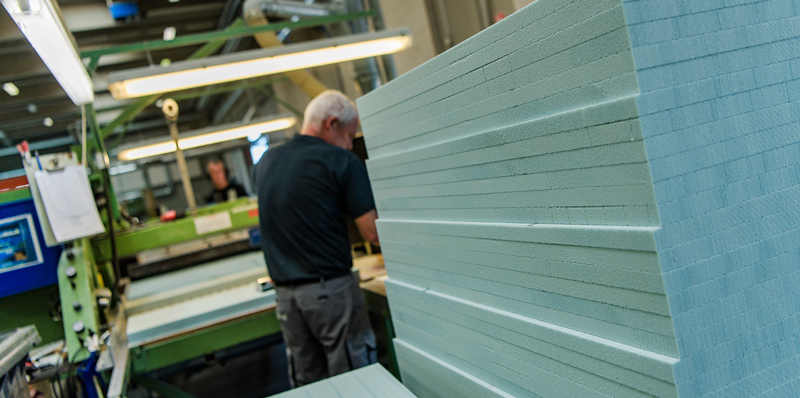
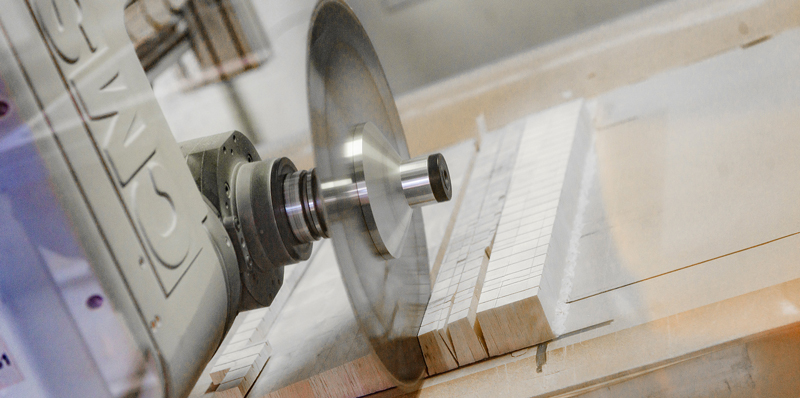
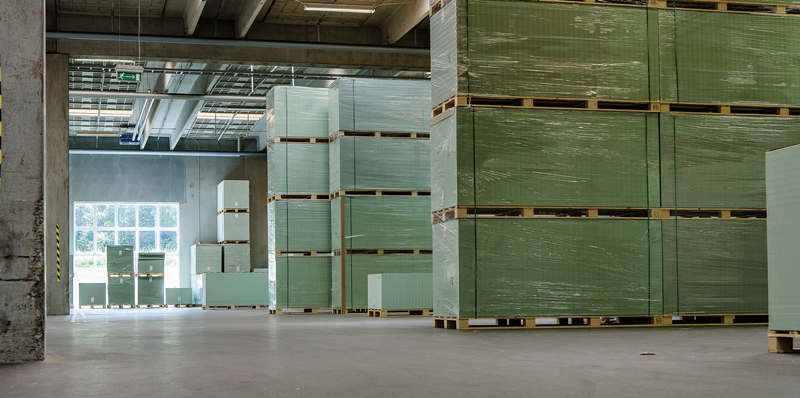
For more than 30 years our Kitting business has supplied core kits to the Wind industry. This experience has led to the optimisation of every step of the kitting process.
We offer a range of sub-suppliers and core materials when working with clients. And our engineers are ready for the iterations of prototyping and testing necessary to deliver a high quality kit which meets the exact specifications and requirements of the project.
To maximise efficiency and agility, Gurit has adopted a strategy of co-locating the production of core materials with the kitting facilities. This saves transportation costs and reduces emissions, as well as enabling the recycling of core waste from the kitting process back into the production of new material.