Case Study
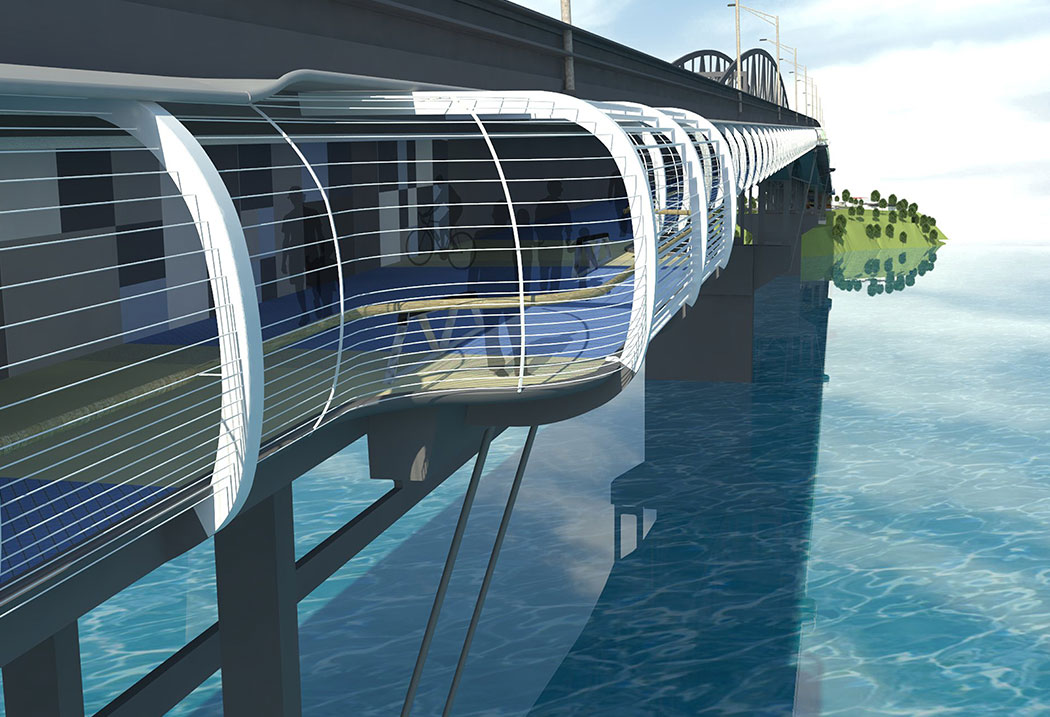
Auckland Harbour Bridge (AHB) has not provided any walking or cycling access since it was built in 1959. The two box girders “clip-on” lanes added in 1969 did not change that as they merely provided additional road traffic capacity. With SkyPath, the famous Auckland harbour crossing will provide a shared walking and cycling path on the city side of the bridge.
SkyPath is the talk of the town. It is being developed and championed by the Auckland Harbour Bridge Pathway Trust, a charitable trust whose aim is to have a world class walking and cycling facility on the AHB. In order to implement SkyPath as a community facility, it is proposed to provide funding by charging fees for users, including tourists, recreational users and commuters. Optimised cost, low maintenance and longevity are obviously very important to a project like this.
The New Zealand Herald applauds that SkyPath will be built out of “space-age materials”. Well, if not tried and tested in outer space, composites certainly have proved their supremacy over traditional building materials in marine and maritime conditions. The Auckland Harbour Bridge Pathway Trust explains: “SkyPath is capitalising on New Zealand’s marine expertise by proposing the use of composite materials and manufacturing technology developed for the America’s Cup.” SkyPath will be constructed by Auckland yacht builders who built the Team NZ and Oracle America’s Cup catamarans. Project Director Bevan Woodward says: “Whilst we’ve had to go through a significant design update and testing programme, we have now achieved a composite solution for a similar price to steel and aluminium construction. This means Sky- Path will be stronger and lighter, will be easier to implement and have much lower maintenance costs with a service life of at least 50 years.”
Over the past decades, the two box girder lanes of the Auckland Harbour Bridge have been the object of significant structural issues, strengthening work and on-going maintenance. As those in the marine industry would be well aware, when a stiffness critical structure requires reduced weight and low maintenance, composite structures have a distinct advantage. Gurit has lent its expertise to provide the Auckland Harbour Bridge Trust, Airey Consultants and Core Builders Composites with a practical solution utilising all the benefits of composite construction.
Core Builders Composites project manager Tim Smyth says: “The use of composite materials for buildings and bridges has been proven overseas. We propose to work with a number of Auckland composite manufacturers in a similar programme as the successful production of the 14 America’s Cup AC45 catamarans.
We would deliver SkyPath in 14 metre long, 4 metre wide sections ready for nightly installation onto the city side of the Harbour Bridge.” According to Gurit’s and Core Builders’ proposal, SkyPath requires over 4000m2 of sandwich panel decking, some 250 10-metre long E-Glass and carbon reinforced ribs.
Gurit has been involved working closely with the team from an early stage developing a composite solution from a newly developed geometry and the loading constraints of the existing steel bridge structure as outlined and studied by Airey Engineering. The conceptual geometry including the main deck / pathway and structural beams and ribs were modelled and a finite element analysis was carried out on the modules in the central navigation span which were deemed to be the most critical due to the lack of available depth. The design of the FRP structure was carried out in accordance with a coherent Limit State methodology with the actions and load combinations taken from a relevant design codes. This design approach has been used by Gurit for the design of a wide range of civil and architectural FRP structures installed around the world using Euro Code or International Building Code to define actions and load combinations.
Global laminate specification was found to be driven by deflection criteria at the Serviceability Limit State. Local reinforcement and additional structure in way of the connections to the steel bridge structure is driven by static strength criteria at ULS. Fire performance was considered and the structural material choices meet NFPA Class B.
This preliminary analysis has led to a conceptual laminate based upon a Gurit® GPET 100 FR foam core with a quadraxial E-glass skins for the path way and beams. The FEA was beneficial in determining the most efficient use of carbon uni-directionals and E-glass unidirectionals in the rib and frame specifications.
A weight and costing study was carried out carefully due to the weight critical requirements of the existing bridge allowing for a comparison and review of the loading to the original metal concept that had been proposed previously. Further development in the full design stage will be needed to extensively review all sections and details but at this concept stage 250 tonnes saving is predicted.
For a project of this scale and given the tight timeline that aims at completing the construction of SkyPath by the end of 2015, the cooperation of the wider New Zealand composite industry will be required. NZ Marine Industry Association’s Peter Busfield says “We believe SkyPath will be an exciting showcase for the NZ marine and composites industries. It will be a high profile demonstration of our expertise that will enable us to talk to many other sectors about utilising our services, and not just in NZ but internationally.”