Case Study
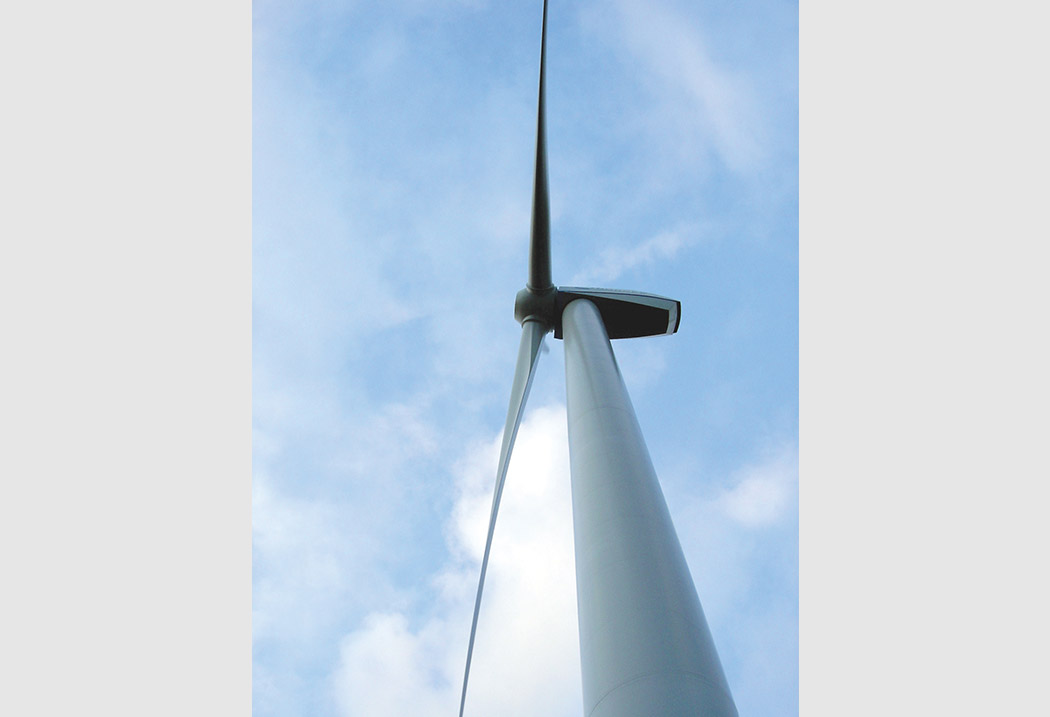
When Danish company SSP Technology A/S set itself the challenge of creating a cost effective 34-metre blade with high yield, superior quality, low weight, and a long life span, it chose to partner Gurit in the areas of structural design and materials specification. The results are impressive..
SSP Technology A/S is a small company making a large impact in the wind energy market. Its first blade project, the SSP 34M, was the concept of co-founders Flemming Sørensen and Rune Schytt-Nielsen.
Gurit’s involvement in the project began in 2002 when a team of Gurit engineers was enlisted to co-operate with SSP’s own engineers on the structural design concept for the blades. Packages such as Finite Element Analysis (FEA) and Laminate Modelling were used to ensure that a lightweight, yet incredibly strong, blade was designed. The need to meet Germanischer Lloyds (GL) certification standard was also of importance.
Following the successful completion of 34M’s structural design,the next step for SSP was to collaborate with Gurit’s account engineering team, in selecting the materials and manufacture process. The objective was to create a robust, repeatable blade manufacturing process, which would ensure consistently high quality blades. It was also critical that the finished blade should be competitively priced and easily produced in a clean working environment, adhering to health and safety regulations.
To meet these requirements, a combination of SPRINT™ and prepreg was selected. The processing properties of SPRINT™, coupled with the recently launched WE 90 prepreg system, would guarantee a robust manufacturing process. A high quality, low void content laminate would be achievable and the resin content of the prepreg controlled at the point of manufacture. Fast deposition rates would also be possible through reduced debulking and an automated cutting process. As no contact with the liquid resin matrix is necessary with WE 90 and SPRINT™, a good level of health and safety during production would be maintained. The only outstanding question was price – could a SPRINT™ and prepreg blade be produced at a competitive market price?
Traditionally, prepregs were not seen a viable option for manufacturers due to the perceived high cost of these materials and processes, when compared to infusion and hand laminating techniques. Both Gurit and SSP companies were keen to dispel this misconception and prove that, in fact, SPRINT™ and prepreg materials can be a cost-effective solution.
WE 90 is a very economical resin matrix developed especially for use with SPRINT™ and other fibres. Although the base chemistry of the WE 90 products remain the same throughout the range of combinations, handling properties and characteristics can easily be adapted to suit the needs of the fabric or fibre a customer requires. To further reduce costs, SSP was able to optimise processes and add some innovative design features to the 34M blade, traditionally associated with post-production processing.
The result of Gurit and SSP’s collaboration speaks for itself. The 34M blade has exceeded all expectations and test criteria, both in the lab and in the field, and is one of only a few blades to endure rigorous static and 20 year dynamic fatigue tests. SSP Technology A/S now has a concept that can easily be adapted to the market’s demand for bigger blades, and the company now possesses a distinct advantage against many competitors.
In December 2003, the first sets of SSP 34M blades were mounted and installed onto five wind turbines in a wind park situated in Northern Germany.