Case Study
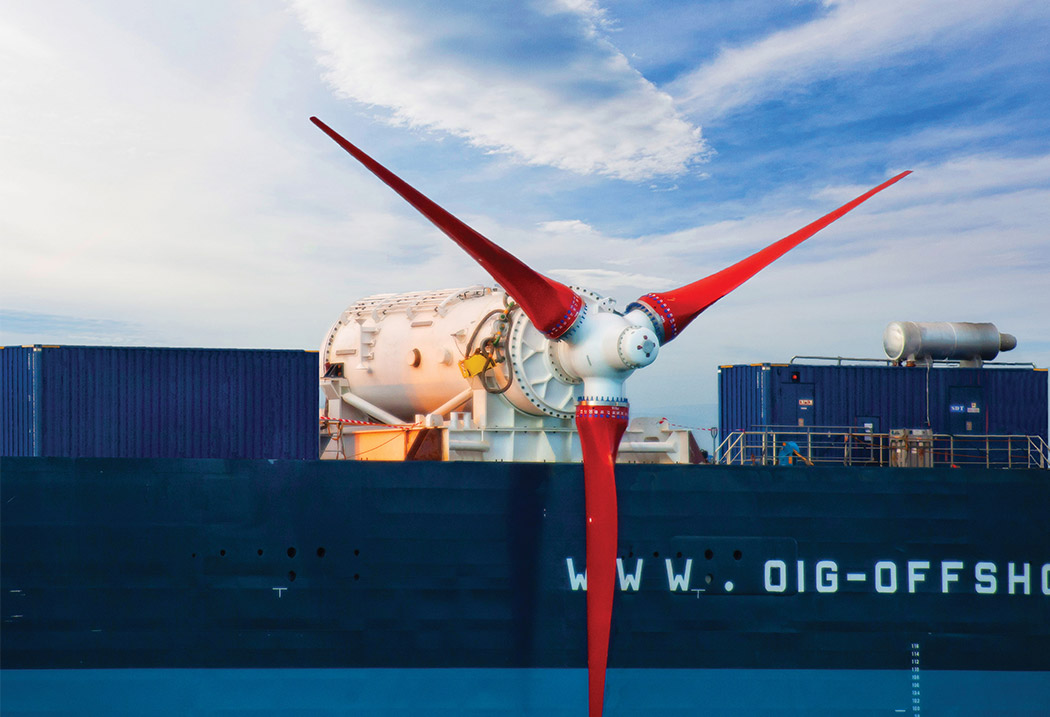
With a rated capacity of 1MW and a diameter of over 20m the ANDRITZ HYDRO Hammerfest HS1000 is the largest single tidal turbine rotor to be installed to date. The 9m tidal blades were engineered and manufactured using Gurit materials by a team at Gurit UK.
The materials used were predominantly from Gurit’s wind energy range including SparPregTM and SPRINTTM, but the high degree of curvature combined with significant laminate thicknesses required the development of new processing and manufacturing techniques to create a finished product with the level of quality required to maintain the high performance for a design life of 25 years. Indeed the design process included a material test programme of over 1,000 individual coupons to ensure that the materials properties in both dry and seawater saturated conditions were well understood in order to provide confidence in the blade integrity even after long term immersion in this aggressive environment.
REFINED STRUCTURE
Gurit worked closely with the customer, ANDRITZ HYDRO Hammerfest, and their chosen partners to ensure that the loadcases and interface requirements for the tidal blades were accurately assessed and also to refine the blade geometry, particularly in the root area to provide the best hydrodynamic performance available while meeting the load bearing requirements of the structure. The resulting geometry and construction methodology ensured that a conventional wind blade concept was not up to the task of withstanding some of the most aggressive tidal streams in the world and a number of novel features were included in the final design.
HIGH QUALITY MANUFACTURING
The four composite tidal blades, 3 for operation on the turbine and 1 for full scale testing, were manufactured in the existing prototyping facility at Gurit UK. The manufacturing timescale limitations and short production run requirements allowed prototype moulds and assembly jigs to be sourced locally and the project saw the facility running at maximum capacity for a significant period of time. The high laminate thicknesses and slender blade geometry ensured that the individual structural components were densely packed with materials, this coupled with the tight timescales placed a high level of focus on achieving the required high quality levels first time every time.
FEEDBACK AND VERIFICATION
Each of the tidal blades was manufactured with integral fibre optic instrumentation to allow AHH to monitor the performance and condition of the blades throughout their lives. This instrumentation is now confirming the predicted performance of the structure and providing valuable real time data that will be used by AHH to check and confirm the design input data and by Gurit to verify the accuracy of the structural analysis
SCALING UP
This project has allowed Gurit to demonstrate its capabilities in structural design and tidal blade manufacture. AHH plan to develop what is expected to be the world’s first tidal turbine array located in the Sound of Islay, again in Scottish waters. This 10MW array has achieved planning consent and turbine design & development is underway demonstrating the rapid growth of this emerging industry.