GURIT HAS BEEN A RELIABLE SUPPLY PARTNER FOR ENGINEERING, MATERIALS AND TECHNICAL SUPPORT TO US FOR OVER 20 YEARS.
OVERVIEW
Industry
Marine
Prepregs, SPRINT™, Engineering
Target
Creating lightweight and high loaded composite components
Solution
Development of SE 84LV; supply of SPRINT™ materials and engineering solutions
Benefits
Ability to build ever larger structures as a result of partnership; shared understanding of environmental responsibility
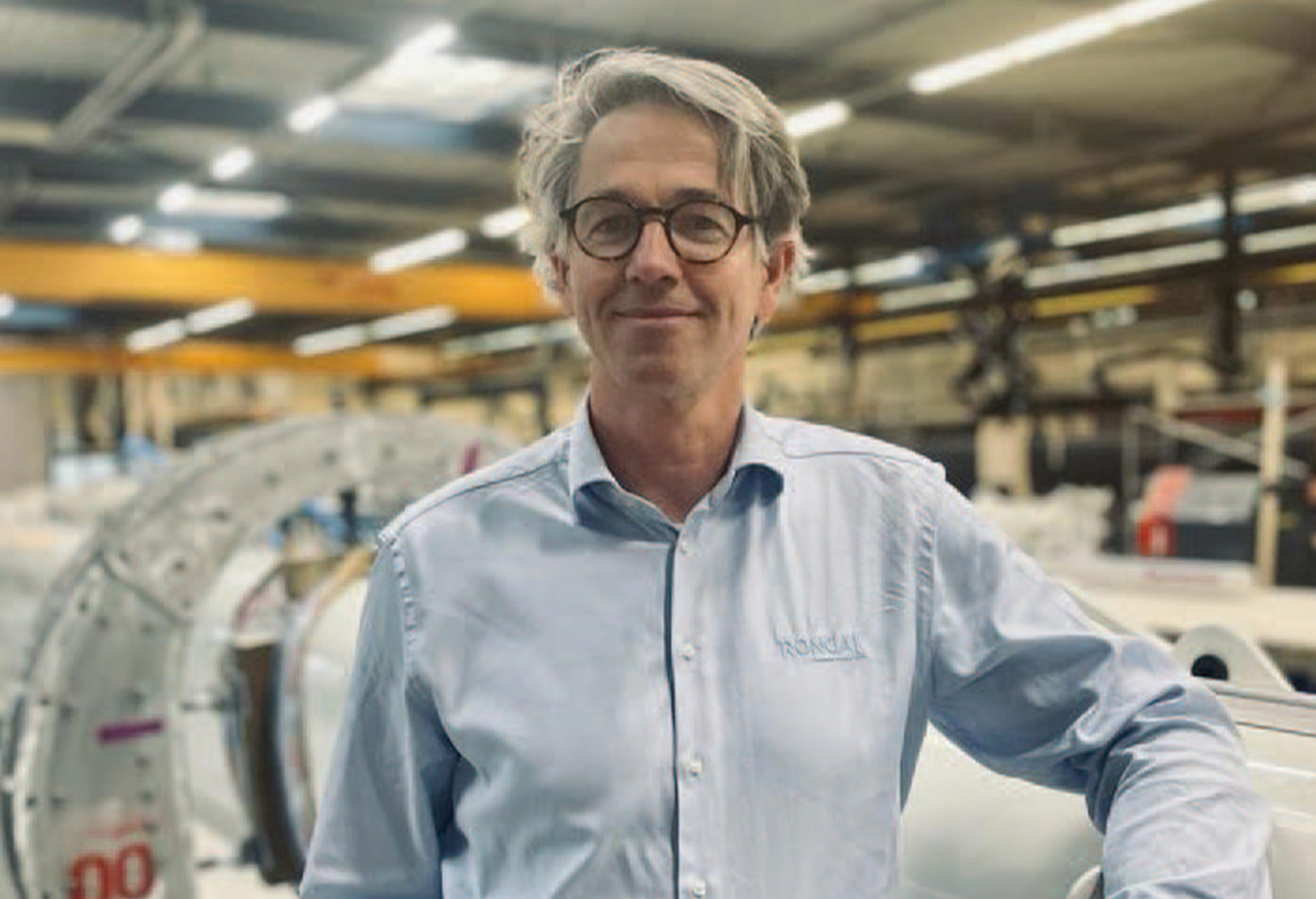
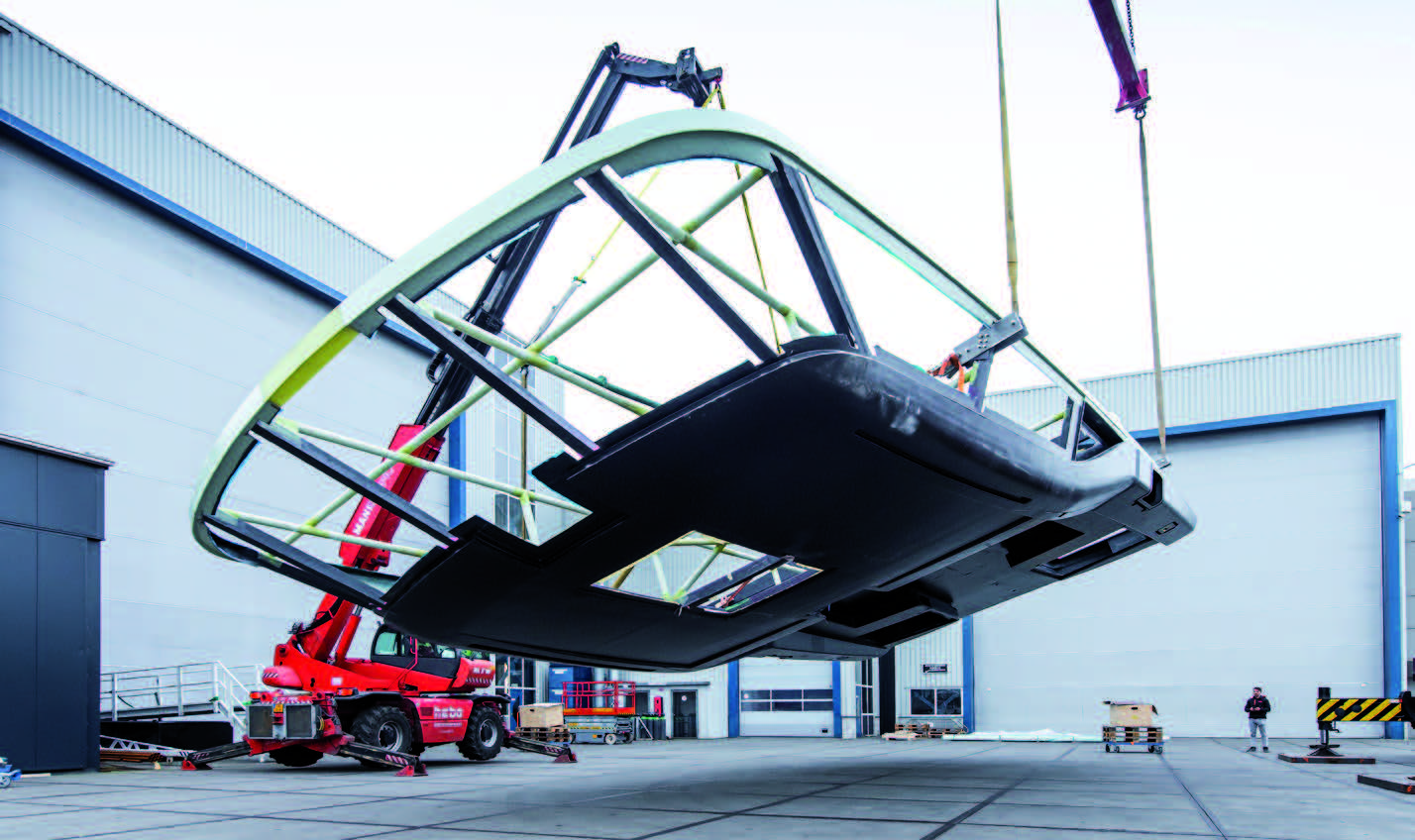
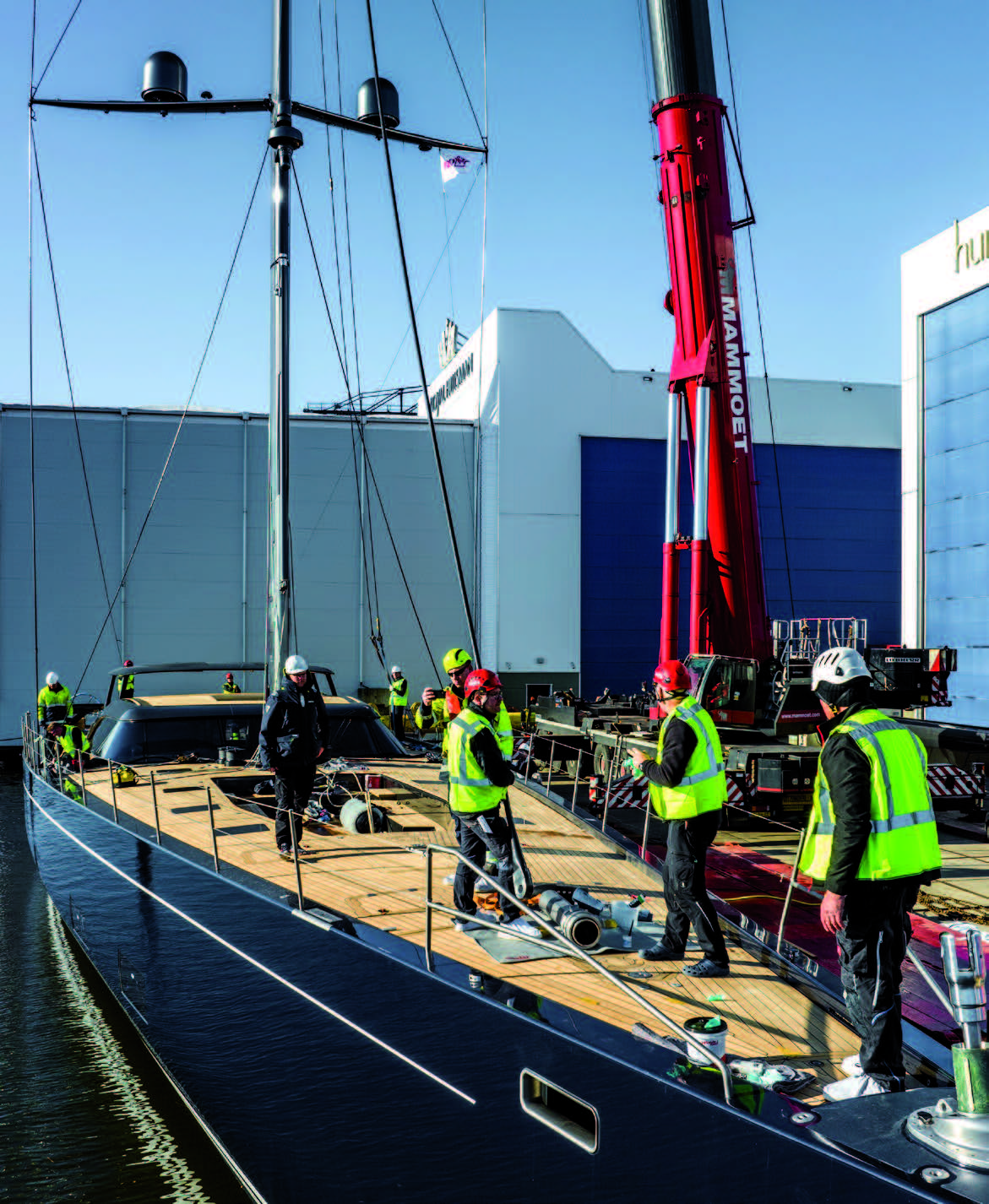
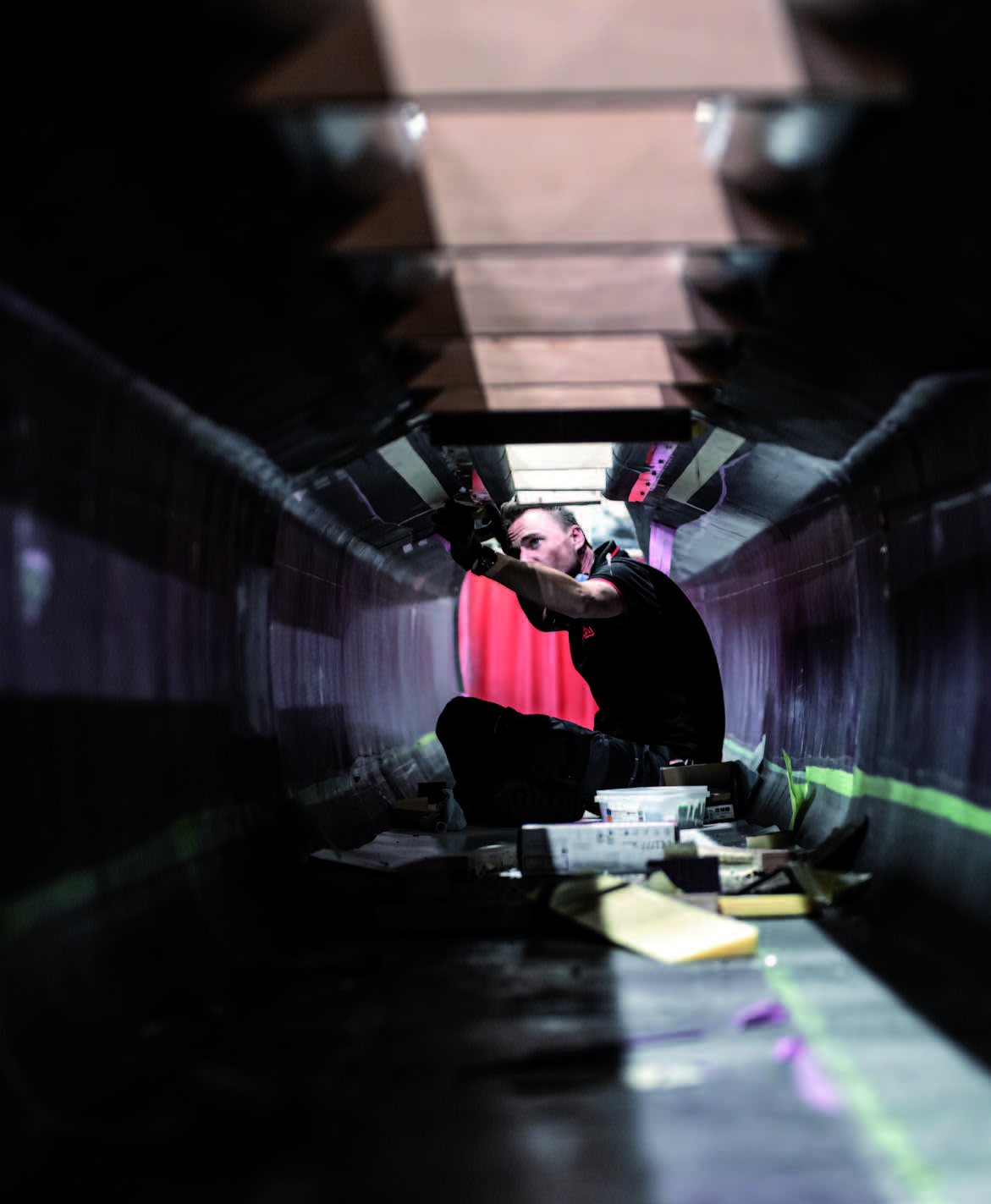
Rondal is located in Vollehove, The Netherlands and is a pioneer in prepreg construction of tall carbon spars and large special parts. Rondal has been using Gurit products for over 20 years, and industry legend SE 84LV was actually developed for their use. The business started as a manufacturer of aluminum spars, hatches and deck equipment; over time it has added captive winches up to 32 tonnes pulling load, carbon hatches and windbreaks. The facility has one of the largest prepreg curing ovens in the world for 70m+ masts, which is currently being extended for even larger ones.
EVER-LARGER PROJECTS REQUIRE RELIABILITY
In the past decade the company has built a number of larger radar masts and superstructures using Gurit structural engineering and SPRINT™ materials. The latter has significantly sped up the production process in comparison to using prepreg whilst still delivering high quality parts. The labour saving over prepreg is significant and cost wise it comes out similar to infusion.
Two such large superstructures have recently been delivered to Royal Huisman Shipyard for sailing yacht projects 404 and 405, the new Nilyala. The use of Gurit composites has not only saved weight but also enabled the designers to use aesthetically pleasing shapes.
Rondal’s products feature on some of the worlds largest superyachts, and have a reputation for durability, reliability and innovation. They therefore work with Gurit which has been a reliable supply partner for engineering, materials and technical support. The Rondal facility is Lloyds, DNV and RINA accredited and as such requires materials which are certified with the same. Together with the Gurit Technical Support team, Rondal has optimised its facilities and processes as their projects become ever larger and more complex.
Rondal also tests laminates for mechanical & thermal properties for each project using Gurit’s test facilities, and Gurit technical support team members are regular welcome visitors to the Rondal facility to discuss processes, new materials or customized solutions.
Rondal has a talented mix of people in their engineering offices and on the shopfloor with experience and building America’s Cup, IMOCAs, Ocean Race and many other high profile yachts. Prior to starting with Rondal they have worked with Gurit materials so they easily integrate and know how the materials and process work.
Rondal continues to invest in optimizing processes with a larger autoclave due to arrive later this year, as well as extension of ovens. They also have a large CNC prepreg cutting machine to optimize use of materials and minimize waste.
Rondal sees that the market for sailing superyachts is on the increase, driven by owners who have become more environmentally conscious while enjoying the action onboard a sailing yacht, but also the competitive spirit of sailing regattas around the world. With the drive for electrification of sail handling systems and the incorporation of solar cells in spreaders and booms, Rondal is poised to work with Gurit to achieve a greener future.